Ringsted / Dykon is a Green Factory
Ringsted Dun is constantly working to reduce the impact on climate, and thus to ensure more efficient resource utilisation. Large parts of the products are made from sustainable and environmentally friendly natural materials. In principle, you can leave your Ringsted Dun down duvet outdoors and it will degrade 100% over time. Of course, we don’t recommend that you do, because we also focus a lot on more sustainable waste management.
The company also aims to become more sustainable in its production. Consumption of water and energy varies according to how busy the production is. New intitiaties are continuously introduced that ensure the reduced consumption of, among other things, water, natural gas and electricity. This way, even lower CO2 consumption can be achieved.
Ringsted Dun also works purposefully with the UN Global Goals. Through their membership of amfori BSCI, the company helps support the UN Global Goals through their foreign suppliers and partners, with a focus on e.g. gender equality and better working conditions.
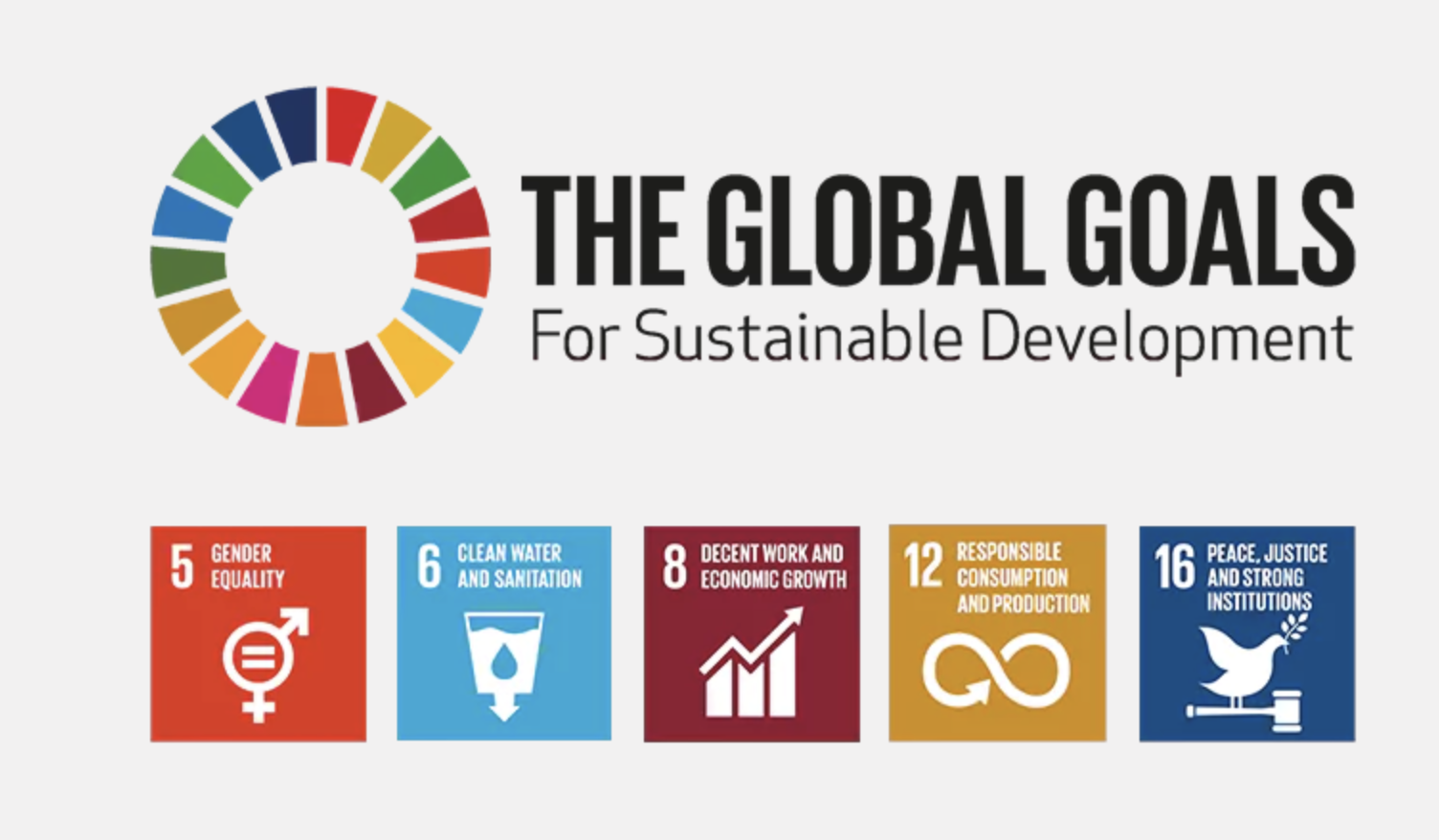
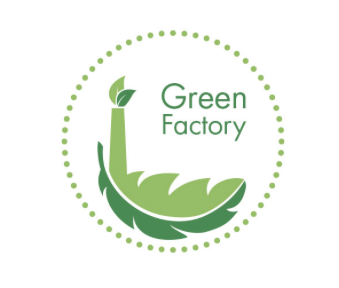
DYKON focus on the environment and sustainability
Large part of the products are made from sustainable and environmentally friendly, natural materials. Their consumption of water and energy varies depending on how busy the factory is. The company is introducing ongoing initiatives that contribute to a lower consumption of water, natural gas and electricity. In this way, DYKON ensures even lower CO2 production.
Below you can read about the initiatives in engird, waster, water and sustainability:
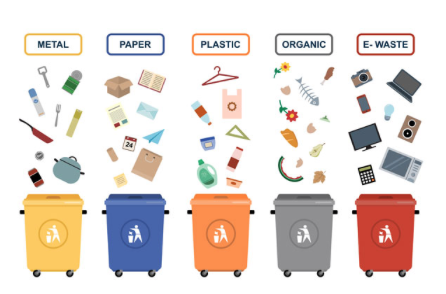
Waste:
A manufacturing company will invariably create waste - our supplier does, too. However, DYKON has decided that its waste must be reused or recycled as new energy or materials. In that way, the company ensures a circular economy, which is as environmentally friendly as possible within the present standards.
The waste is divided into 6 main categories: combustible, cardboard, clear plastic, Strapex straps, metal and iron as well as electronic.
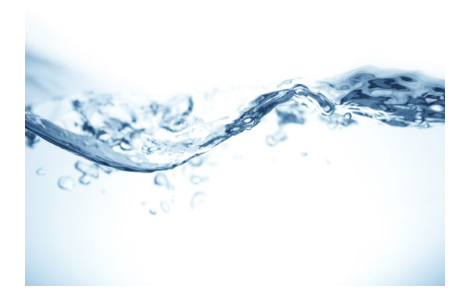
Recycling:
Combustible waste is converted into district heating at the local incineration plant. In that way, the factory is integral in providing heating for all the district heating customers of the local community. Cardboard, clear plastic and Strapped straps are sorted into individual categories and recycled. Metal and iron is collected and reused in new materials, of which metal and iron form part.
This is one of the ways, DYKON ensures that its carbon footprint is kept at the absolute minimum.
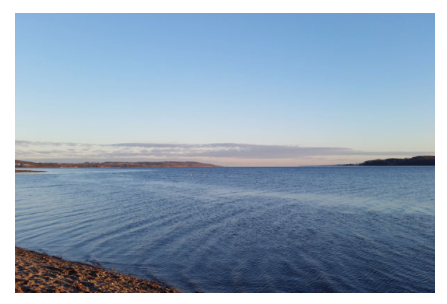
Water in the production:
Water is a raw material that is essential to producing duvets and pillows. Without water, DYKON would not be able to wash their down and feathers in the washing line. Even though in Denmark, they are lucky enough to have access to clean underground water, it is important for DYKON to reduce water consumption. The company considers water a precious resource that is to be upheld.
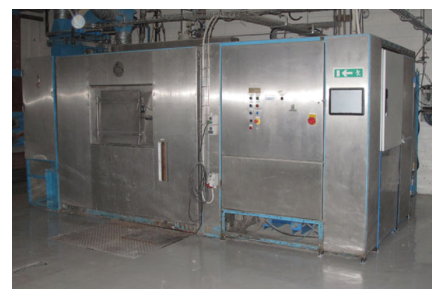
Private Water Bore:
DYKON is lucky to have its own water bore at its disposal. In fact, they have two bores, both of which established in 1971. In 2006, they decided to shut down one of their wells, as they do not consume that much of water!
Having their own water bore also means that DYKON is responsible for maintaining and renovating the well. This is done in accordance with Danish regulations, and an external company performs regular inspections of the water bore.
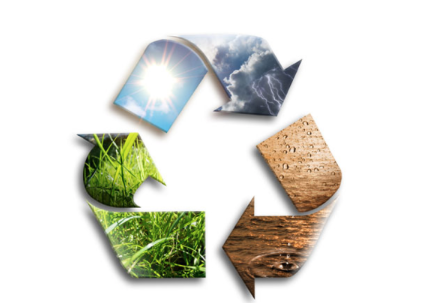
Waste Water:
DYKON consumes rather large amounts of water in its laundry. It's called process water: at each wash, DYKON adapts the amount of water and soap, so that they use neither too little, nor too much water. The factory discharges waste water at night to avoid putting too much strain on the local sewage system. It's then purified at the wastewater treatment plant in the neighboring village, Vamdrup, where they clean the sewage water from the entire local area.
DYKON's vision for the future is to become able to recycle the processes water in a circular system. They are currently working with a local company that is specialized in such processes, to design a system that would allow to reduced water consumption further.

Grander Water:
DYKON has made great progress in terms of water consumption, using technological automation and digitalization. One initiative is their GRANDER water system: "Grander Water Revitalizing System".
The GRANDER system changes the state of the water molecules which causes the water to find its optimal rest position before entering our washing processes. The reduction in the surface tension has given rise to several changes at DYKON.
- the consumption of soap in the laundry has reduced by 32% in the first year
- pipes and condensers were free of internal coatings, such as corrosion and deposits
- previously, the water was dirty and emitted a bad odour after having passed through our washing process. Now, it is odor-free and looks clean afterwards.
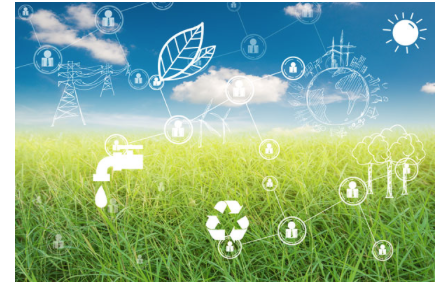
Energy Optimization:
A manufacturing company such as DYKON uses engird in the form of heat and electricity. Its consumption varies in accordance with the work load. The company introduces initiatives on an ongoing basis, which contribute to a lower consumption of natural gas and electricity, amongst others. In that way, DYKON ensures that they leave an even lesser carbon footprint.
Concrete examples of improvements carried out in the manufacturing are e.g. the introduction of energy-efficient LED lights, changing our boiler, checking and insulating pipes in the wash line and continuously digitalising and automating more manufacturing processes.
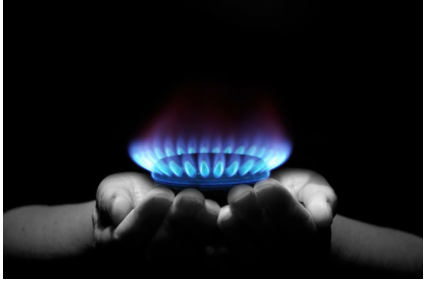
Natural Gas:
DYKON uses a pure energy source: Natural gas.
The consumption by manufacturing, respectively, varies according to the level of activity and the consumption by heating varies according to the season. We continuously aim to improve our natural gas consumption. Here automation and digitalisation play a part once more. DYKON has made the following concrete initiatives to reduce its natural gas consumption:
- all of their pipes have been tested for leaks and have been isolated. This led to a saving of 14 percent
- a replacement of its gas boiler has reduced the use of natural gas by 27 percent!